In modern industry, every detail improvement can bring remarkable results. For those who pursue high precision and high efficiency, a high-quality step drill is undoubtedly an indispensable helper.
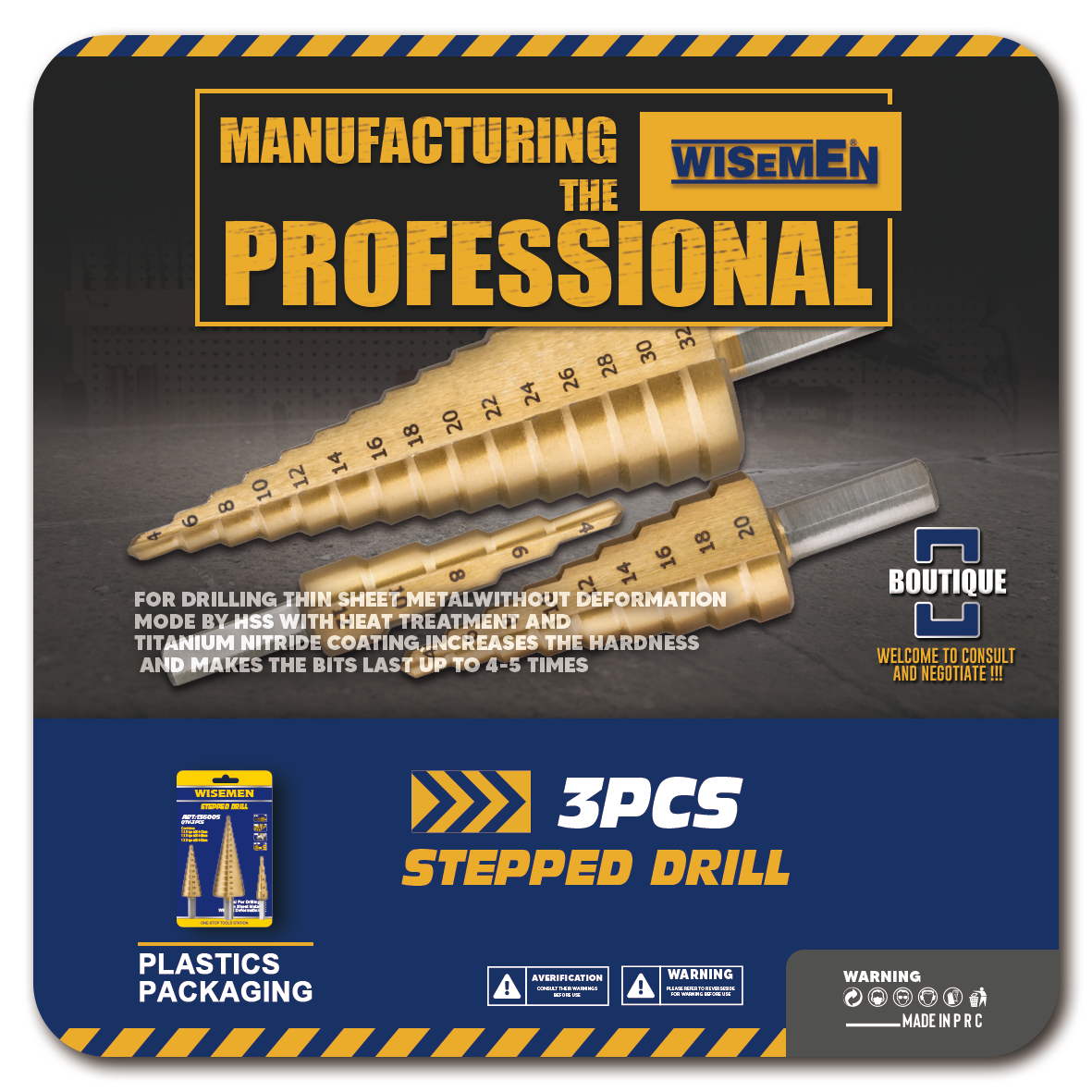
First, let's explore the unique features of the step drill. As a professional tool designed for deep processing, it has the characteristics of progressive layer by layer. It can complete multiple holes with different diameters at one time during drilling, which greatly improves work efficiency. At the same time, due to the design concept of its special structure, the vibration generated in the cutting process is reduced to a minimum, and the surface of the finished product is smooth and flawless.
Not only that, the scope of application of the step drill is also very wide. Whether it is hard metal materials such as steel, or relatively soft and easy to damage the wood plate, are able to cope with a variety of challenges. Especially in the automobile manufacturing industry, the demand for small apertures at the assembly positions of precision parts inside the engine block is particularly prominent; in the field of furniture customization, it is more reflected in the convenience and accuracy of the fixed installation of the connecting parts. Played an important role.
However, it is worth noting that not all step drills are suitable for every working environment. Therefore, when we are ready to purchase such a piece of equipment, we must consider several key factors-the first is the material selection problem. At present, there are high-speed steel (HSS), hard alloy coating (TiN/TiCN) and other composite strengthening treatments in the mainstream of the market. Among them, the former has lower cost but relatively poor wear resistance; the latter has a longer service life and can adapt to more demanding operating conditions although the initial investment is larger.
There are also specifications matching is also very important. Different thickness of the target object required by the length of the tool is not the same, too short may lead to frequent replacement in the middle of the increase in labor intensity and also increase the risk of error; If it is too long, it is easy to bend and deform due to its own gravity, thus affecting the overall effect. Therefore, it is particularly necessary to make reasonable judgments based on the actual situation after determining the specific needs.
In order to maximize your investment, please remember to follow the correct maintenance procedures to extend the expiration date of this type of equipment. Regular cleaning and removal of residual debris to prevent blockage and aggravation of heat damage to the component body; timely application of lubricating oil to reduce friction resistance and protect the smooth operation of the transmission system are all effective measures.
Finally, let's take a look at a real success story to share. In the past, a small mechanical processing plant has been relying on manual methods to polish the cylindrical grooves on the molded parts one by one, which takes a lot of time and manpower, but it is difficult to reach the ideal standard. Since the introduction of a number of high-end configuration version of the new step drill after not only greatly shorten the production cycle and product quality has been significantly improved won the praise of customers.
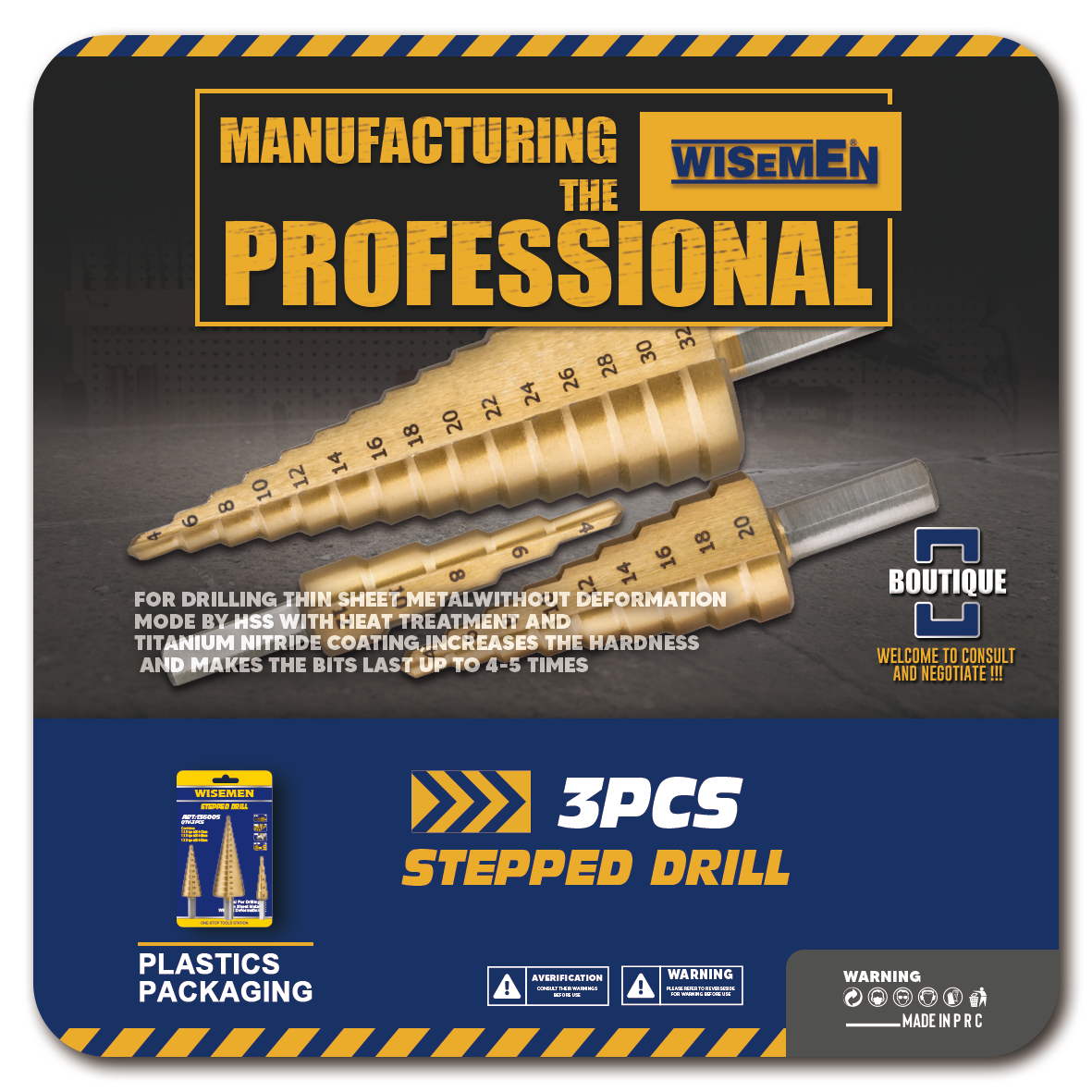